آشنایی با جوشکاری اکسی استیلن
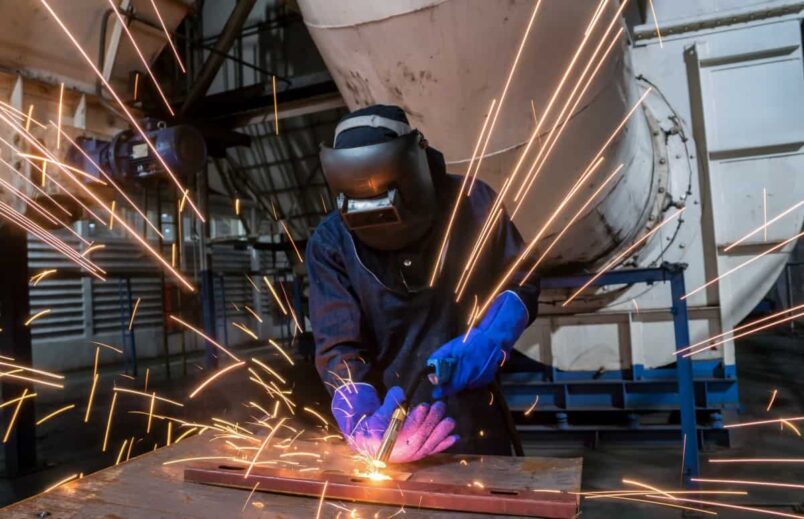
جوشکاری با گاز یکی از قدیمیترین تکنیکهای حرارتی برای اتصال فلزات به شمار میرود که در آن از اکسیژن و گاز سوختنی بهره میگیرند. در گذشته، این روش تقریباً تنها راه تولید جوشهای باکیفیت در اکثر فلزات صنعتی محسوب میشد.اما با گذشت زمان، تکنیکهای نوین جوشکاری به وجود آمدند که به دلیل کارایی بیشتر، کیفیت بالاتر و عملکرد بهتر در چندین زمینه، جایگزین این روش قدیمی شدهاند.
با این حال، فرایند جوشکاری گازی به خاطر سهولت و تنوع بالای کاربردها، همچنان در میان علاقهمندان و کارگاههای کوچک فلزی محبوبیت خود را حفظ کرده است. اما امروزه، استفاده از این روش عمدتاً به ورقهای نازک و فعالیتهای تعمیراتی محدود شده است.
جوشکاری گازی چیست؟
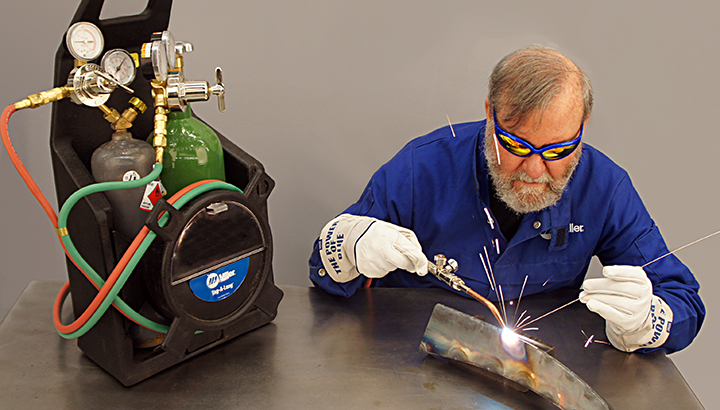
آشنایی با جوشکاری اکسی استیلن
جوشکاری گازی که به عنوان جوشکاری اکسیسوختی نیز شناخته میشود، روشای است که در آن با بهرهگیری از حرارت ناشی از سوختن ترکیبی از گازها، فلزات ذوب شده و به یکدیگر متصل میگردند. هرچند که میتوان قطعات فلزی را بدون استفاده از مواد پرکننده به هم پیوند داد، اما به کارگیری سیمهای پرکننده به منظور افزایش استحکام و ماندگاری جوش، توصیه میشود.
برخلاف بیشتر فرآیندهایی که برای تولید حرارت به الکتریسیته وابستهاند (مانند جوشکاری قوس الکتریکی MIG، TIG و SMAW)، در جوشکاری گازی، شعله تنها از طریق احتراق یک ترکیب گازی ایجاد میشود. اکسیژن و استیلن به عنوان ترکیب اصلی این گازها شناخته میشوند، زیرا در تولید حرارت برای جوشکاری فولاد بسیار کارآمد هستند. به همین خاطر، این نوع جوشکاری به نام جوشکاری اکسیسوختی یا اکسیاستیلنی معروف است.
سوختهای دیگری چون پروپان، هیدروژن و گاز کوره نیز در این فرآیند به کار میروند. این ترکیبات برای جوشکاری فلزات غیرفلزی و مصارف خاصی از جمله لحیمکاری قوی و لحیمکاری نقره مناسب هستند.
برای برش اکسیاستیلنی، از تجهیزاتی مشابه جوشکاری اکسیژن بهرهبرداری میشود، به شرطی که مشخصات شعله تنظیم شده و یک قطعه برش نسبتا مقرون به صرفه به آن افزوده شود. مشعل برش دارای ماشهای است که اکسیژن را به صورت انفجاری آزاد کرده و به فرآیند ذوب و خروج فلز مذاب کمک میکند.
جوشکاری اکسیژن – سوختی
جوشکاری با استفاده از اکسیاستیلن به تولید حرارت از احتراق ترکیب اکسیژن و گاز سوخت وابسته است. این گازها که در سیلندرهای فشرده نگهداری میشوند، از طریق شلنگهای قابل انعطاف (یک شلنگ برای اکسیژن و یک شلنگ برای گاز سوخت) و با تنظیم رگلاتورهای مخصوص به جریان درمیآیند. سپس، این گازها در محفظه ترکیبی مشعل دستی اکسیژن-سوخت به هم میآمیزند و از طریق دهانه نوک مشعل خارج میشوند. اندازه دهانه نوک جوشکاری از اهمیت ویژهای برخوردار است و باید با توجه به نوع کاربری به دقت انتخاب گردد.
با گرم کردن فلز پایه، به دمای ذوب (حدود ۳۲۰۰ درجه سانتیگراد) میرسیم که در این شرایط جوشکاری ذوبی انجام میگیرد. تکنیکهای دیگر جوشکاری که از جریان برق بهره میبرند، قادرند به دماهای بسیار بالاتر (بیش از ۵۰۰۰ درجه سانتیگراد) دست یابند، که این امر جوشکاری اکسیاستیلن را برای فلزات نازک مناسبتر میسازد. استفاده از سیمهای پرکننده به صورت اختیاری است و بستگی به نیازهای پروژه دارد.
با توجه به اینکه جوشکاری گازی به مواد سوختنی مرتبط است، رعایت اصول ایمنی مناسب از اهمیت بالایی برخوردار است.
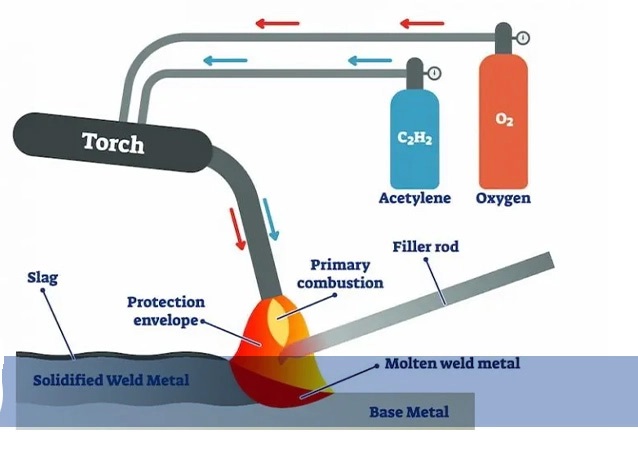
آشنایی با جوشکاری اکسی استیلن
انواع شعله در جوشکاری
شکل و نوع شعله در فرآیند جوشکاری تأثیر بسزایی بر کیفیت و ویژگیهای اتصال جوش دارد. با تنظیم نسبت گاز سوختنی به اکسیژن، میتوان به تغییرات در فرم شعله دست یافت.
افزایش میزان اکسیژن میتواند به ایجاد شعلهای با حرارت بیشتر منجر شود که این امر میتواند سبب تغییر شکل فلز گردد. از سوی دیگر، شعلهای با دما پایینتر هنگامی به وجود میآید که مقدار گاز سوختنی از اکسیژن بیشتر باشد، که این وضعیت ممکن است به کاهش کیفیت جوش منتهی شود.
شعله خنثی
در شعله نوع خنثی، مقدار گازهای مورد استفاده در فرآیند جوشکاری به صورت مساوی وجود دارد. احتراق کامل گاز سوختی و اکسیژن فشرده به این معناست که ویژگیهای فلز جوش تغییر نمیکنند و همچنین میزان دودی که تولید میشود، بسیار ناچیز است.
این شعله جوشکاری شامل دو منطقه است: یک منطقه داخلی به رنگ سفید که دمای آن به حدود ۳۱۰۰ درجه سانتیگراد میرسد و یک منطقه خارجی به رنگ آبی که دمای آن تقریباً ۱۲۷۵ درجه سانتیگراد است. برای جوشکاری فلزاتی نظیر چدن، فولاد نرم و فولاد ضد زنگ، استفاده از شعله خنثی اولویت دارد.
شعله کربنیزاسیون
شعله کربنیزاسیون یا کاهنده زمانی شکل میگیرد که میزان گاز سوختنی بیشتری نسبت به اکسیژن خالص فراهم شود. این نوع شعله به دلیل تولید دوده، دودزا محسوب میشود و با ایجاد کاربید فلزی، آرام و ملایم است.
در این آتش، سه ناحیه مختلف شکل میگیرد: ناحیه مرکزی سفید با دمای ۲۹۰۰ درجه سانتیگراد، ناحیه میانی قرمز که دمای آن ۲۵۰۰ درجه سانتیگراد است، و ناحیه خارجی آبی که دمای آن به ۱۲۷۵ درجه سانتیگراد میرسد. شعله کربنیزاسیون بهعنوان گزینهای مناسب برای جوشکاری نیکل، آلیاژهای فولادی و فلزات غیرآهنی به شمار میآید.
شعله اکسیدکننده
زمانی که گاز اکسیژن از سیلندر بیشتر از مقدار گاز سوختنی موجود باشد، شعلههای اکسیدکننده شکل میگیرند. این افزونگی اکسیژن باعث افزایش دمای شعلهای میشود که از مشعل خارج میگردد، در مقایسه با شعلهای که در شرایط خنثی تولید شده است.
این نوع شعله شامل دو بخش است: یک ناحیه داخلی به رنگ سفید که دمای آن به حدود ۳۵۰۰ درجه سانتیگراد میرسد و یک ناحیه خارجی آبی که دمای آن به ۱۲۷۵ درجه سانتیگراد میباشد. شعله اکسیدکننده برای جوشکاری فلزاتی نظیر برنج، مس، برنز و روی مورد استفاده قرار میگیرد.

آشنایی با جوشکاری اکسی استیلن
انواع تکنیکهای جوشکاری
از انواع تکنیکهای جوشکاری میتوان به موارد زیر اشاره نمود:
-
جوشکاری چپرو
در این شیوه، مشعل به سمت چپ از راست اتصال حرکت میکند و نوک آن با قطعه کار زاویهای بین ۶۰ تا ۷۰ درجه تشکیل میدهد. ماده پرکننده نیز در زاویهای بین ۳۰ تا ۴۰ درجه نسبت به سطح قرار میگیرد. انجام سه حرکت دایرهای، چرخشی یا جانبی باعث ایجاد ذوب یکنواخت در شعله میشود.
جوشکاری چپرو به طور عمده برای متصل کردن صفحات صاف با ضخامت حداکثر ۵ میلیمتر، چدن و نیز فلزات غیرآهنی به کار میرود.
-
جوشکاری راسترو
در مقابل جوشکاری چپرو، فرآیند راسترو از سمت چپ نقطه اتصال شروع شده و به سمت راست ادامه مییابد. زاویه بین نوک مشعل و قطعه کار در حدود ۴۰ تا ۵۰ درجه قرار دارد و زاویه میان سیم پرکننده و ماده پایه نیز بین ۳۰ تا ۴۰ درجه است.
جوشکاری راسترو معمولاً از نظر سرعت نسبت به جوشکاری چپرو برتری دارد و همچنین میزان اعوجاج و مصرف سیم پرکننده در آن کمتر است. این تکنیک قادر به تولید جوشهای متراکمتر و مستحکمتری است که برای جلوگیری از آلودگی کارایی مناسبی دارند.
-
جوشکاری راستگرد تمام وضعیت
این روش ترمیمی به جوشکاری راستگرد مربوط میشود و بهویژه برای جوشکاری ورقهای فولادی و همچنین تعدادی از لولهها و جوشهای لببهلب با ضخامت بین ۵ تا ۸ میلیمتر کاربرد دارد. در این تکنیک، امکان دید و حرکت کامل الزامی است.
-
جوشکاری عمودی
در این شیوه، با حرکت نوسانی الکترود و مشعل از پایین به سمت بالا، درز جوش تشکیل میشود. الکترود با زاویه ۳۰ درجه و مشعل با زاویهای بین ۲۵ تا ۹۰ درجه نسبت به قطعه کار، بسته به ضخامت آن، قرار میگیرد.
برای ورقهای فولادی با ضخامت حداکثر ۵ میلیمتر، یک اپراتور قادر است از این روش بهرهبرداری کند، اما برای فلزات با ضخامت بیشتر، به همکاری دو اپراتور نیاز است.
مواد قابلاستفاده:
- آلومینیوم
- برنج
- برنز
- فولادهای کربنی
- چدن
- مس
- منیزیم
- فولاد نرم
- نیکل
- فولاد ضدزنگ
- آلیاژهای فولاد
- روی
مزایای جوشکاری گازی
- این روش برای انواع مختلف فلزات شامل آهن و فلزات غیرآهنی قابل استفاده است.
- جوشکاری گازی نیازی به برق ندارد.
- این یک تکنیک جوشکاری ساده و مستقیم است.
- ابزارهای جوشکاری گازی نسبت به دیگر روشهای جوشکاری از نظر هزینه به صرفهتر و از لحاظ حمل و نقل آسانتر هستند.
معایب جوشکاری گازی
- جوشکاری گازی نسبت به روشهای جوشکاری قوسی مانند TIG و MIG، حرارت و عمق نفوذ کمتری را فراهم میآورد.
- این مرحله به پرداخت پس از جوشکاری احتیاج دارد تا جلوهای زیباتر و جذابتر به محصول ببخشد.
- جوشکاری با استفاده از اکسی استیلن احتمال بروز نقصهای جوش را به همراه دارد، چرا که از حوضچه جوش به درستی محافظت نمیشود.
- جوشکاری گازی به لحاظ سرعت گرمایش و خنککنندگی، نسبت به تکنیکهای پیشرفتهتر، عملکردی کندتر دارد.
- این نوع جوشکاری برای فولادهای با استحکام بالا مناسب نیست، زیرا ممکن است ویژگیهای مکانیکی آن را تحت تأثیر قرار دهد.
جمعبندی
جوشکاری اکسی-سوختی یکی از نوآوریهای کلیدی دوران انقلاب صنعتی به شمار میرود و در حوزههای مختلف کاربردهای متنوعی دارد. هرچند که امروزه به اندازه گذشته در صنایع مختلف به کار نمیرود و تکنیکهای جدیدتر و پیشرفتهتری جایگزین آن شدهاند، اما این روش همچنان برای برخی از کاربردها به عنوان گزینهای مطمئن شناخته میشود و توسط تعدادی از علاقهمندان و حرفهایها مورد توجه قرار دارد.
مطالب مرتبط: