رازهایی درباره جوشکاری CO2
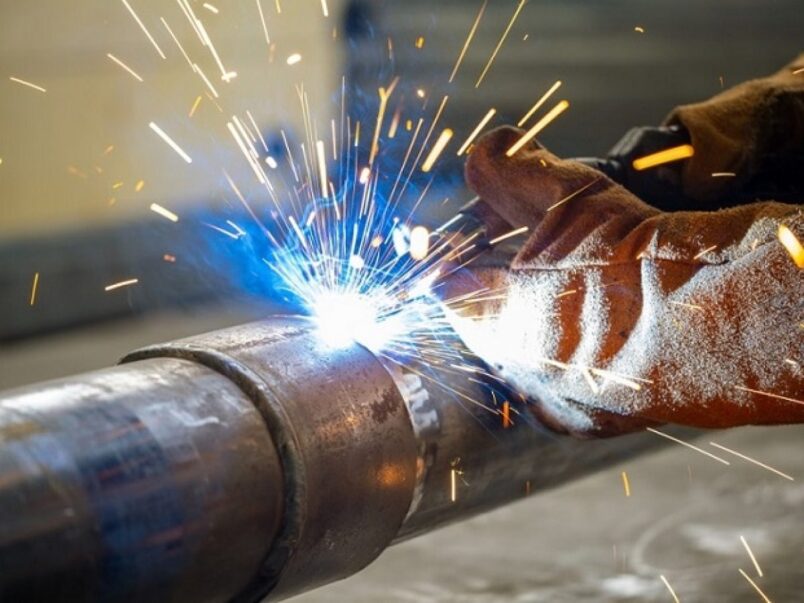
رازهایی درباره جوشکاری CO2
تاریخچه جوشکاری قوسی فلز گاز، که به آن جوشکاری CO2 یا میگ و مگ نیز گفته میشود، به سال ۱۹۲۰ میلادی برمیگردد. در این روش، از یک قوس الکتریکی میان حوضچه مذاب و فلز پرکننده بهرهبرداری میشود.
زمانی که این روش به مرحله تجاری رسید، به اواخر دهه ۱۹۴۰ میلادی تعلق دارد. در آغاز، برای جوشکاری آلومینیوم و با استفاده از گازهای محافظ خنثی مانند آرگون و هلیم، از تکنیک جوشکاری فلز – گاز خنثی (MIG) بهرهبرداری شد. با گذشت زمان، پیشرفتهای حاصل در این زمینه منجر به استفاده از گاز فعال دیاکسید کربن برای جوشکاری فولادها گردید و روش جدیدی به نام جوشکاری فلز گاز فعال (MAG) به میدان آمد.
به تازگی به خاطر قابلیت به کارگیری هر دو نوع گاز خنثی و فعال، اصطلاح جوشکاری قوسی فلز گاز GMAW به طور رسمی برای هر دو فرایند پیشنهاد و تأیید گردید.
درباره جوشکاری CO2
این روش میتواند به صورت نیمهخودکار یا کاملاً خودکار اجرا شود. بسیاری از فلزات با اهمیت تجاری از جمله فولادهای کربنی با استحکام بالا، فولادهای زنگ نزن کم آلیاژ، آلومینیوم، مس، تیتانیوم و آلیاژهای نیکل را میتوان با این تکنیک در انواع شرایط و وضعیتها و با انتخاب مناسب گاز محافظ و الکترود جوشکاری نمود.
شماتیکی درباره جوشکاری CO2
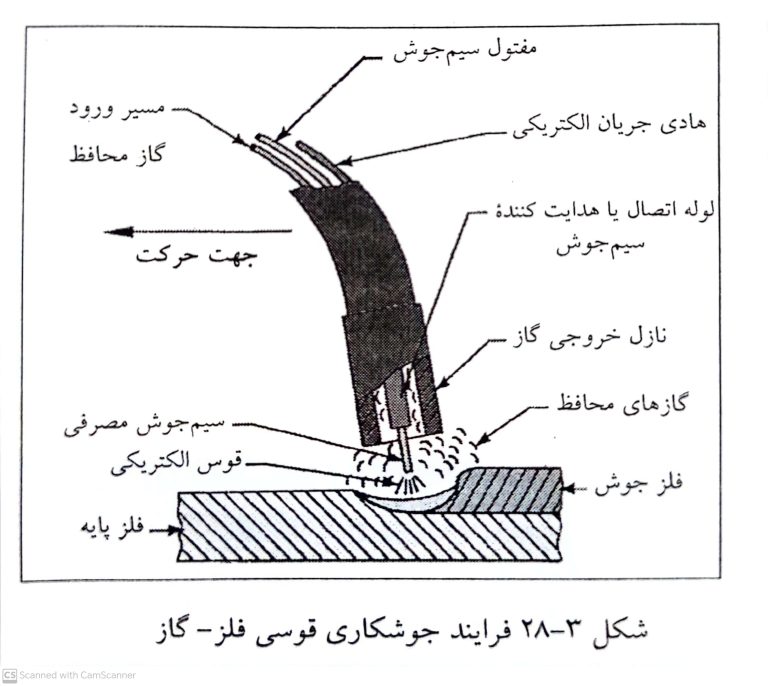
شماتیکی درباره جوشکاری CO2
در این روش، از سیستمهای خودکار برای تغذیه سیم جوش به حوضچه مذاب بهرهبرداری میشود. در این حالت، سیم جوش با استفاده از یک گاز محافظ، ایمن میگردد. قبل از شروع کار، جوشکار یا اپراتور باید بر اساس نوع و ضخامت فلز پایه و سیم جوش، تنظیماتی مانند ولتاژ و سرعت تغذیه سیم جوش به حوضچه را در دستگاه اعمال کند تا طول قوس و جریان الکتریکی بهصورت خودکار مدیریت شود.
پس از آن، جوشکار باید به صورت دستی تنظیماتی نظیر سرعت و جهت جوشکاری و وضعیت نگهداری تورچ را انجام دهد تا هم روند جوشکاری آسانتر گردد و هم جوش با کیفیتی تولید شود. تجهیزات ضروری برای فرآیند GMAW در تصویر ۳-۲۹ نمایش داده شده است. این تجهیزات اصلی شامل تورچ جوشکاری و کابلهای آن، واحد تغذیه الکترود، منبع انرژی و سیلندر یا منبع گاز محافظ است.
شکل شماتیک تجهیزات جوشکاری CO2
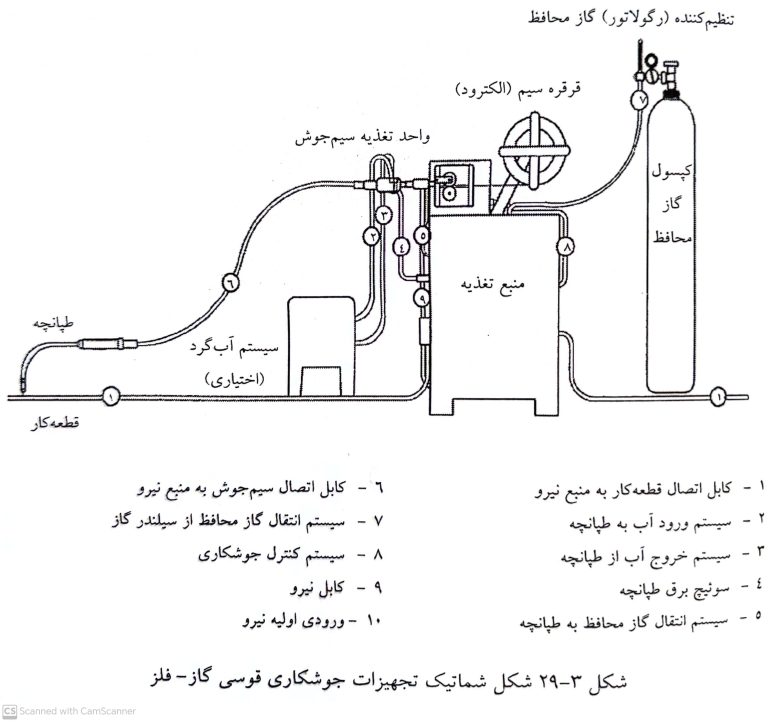
شکل شماتیک تجهیزات جوشکاری CO2
وظیفه تورچ جوشکاری، اتصال سیم جوش به منبع الکتریکی و گاز محافظ و هدایت آنها به سمت قطعه کار است. این فرآیند به ایجاد قوس الکتریکی با انرژی مناسب کمک کرده و از حوضچه مذاب در برابر محیط محافظت میکند. به طور معمول، برای فراهم کردن شرایط خودتنظیم در قوس الکتریکی که راحتی در جوشکاری را به ارمغان میآورد، از منابع تغذیه با ولتاژ ثابت بهرهبرداری میشود. در حقیقت، ایجاد ولتاژ ثابت در یک سرعت تغذیه مشخص، تغییرات در وضعیت یا ارتفاع تورچ را به تغییر در جریان مصرفی مرتبط میسازد تا طول قوس به طور مستمر ثابت بماند.
نحوه عملکرد جوشکاری CO2
بعد از ایجاد قوس الکتریکی و فاصله گرفتن تورچ از سطح قطعه کار، طول قوس حفظ میشود و در نتیجه شدت آمپراژ کاهش مییابد. این افت آمپراژ منجر به کاهش نرخ ذوب سیم جوش میشود. در شرایطی که تغذیه سیم جوش با سرعت ثابت انجام میگیرد، کاهش سرعت ذوب سیم، موجب افزایش طول آن و پیشروی سیم جوش به سمت طول اولیه قوس میگردد و در این حالت ثابت باقی میماند. یکی از عوامل حیاتی در این نوع فرآیندهای جوشکاری، روش انتقال قطرات مذاب سیم جوش به حوضچه مذاب است.
روش انتقال قطرات تحت تأثیر چندین عامل قرار دارد، از جمله اندازه و نوع جریان الکتریکی در قطر سیم، ترکیب شیمیایی جوش، میزان پیش آمدگی سیم جوش از نازل و نوع گاز محافظ. این انتقال به سه روش اصلی صورت میگیرد که در ادامه به توضیح آنها خواهیم پرداخت؛
(الف) انتقال اتصال کوتاه Short circuiting transfer)
ب انتقال قطره ای (Globular transfer)
ج) انتقال اسپری یا پاششی (Spray transfer)
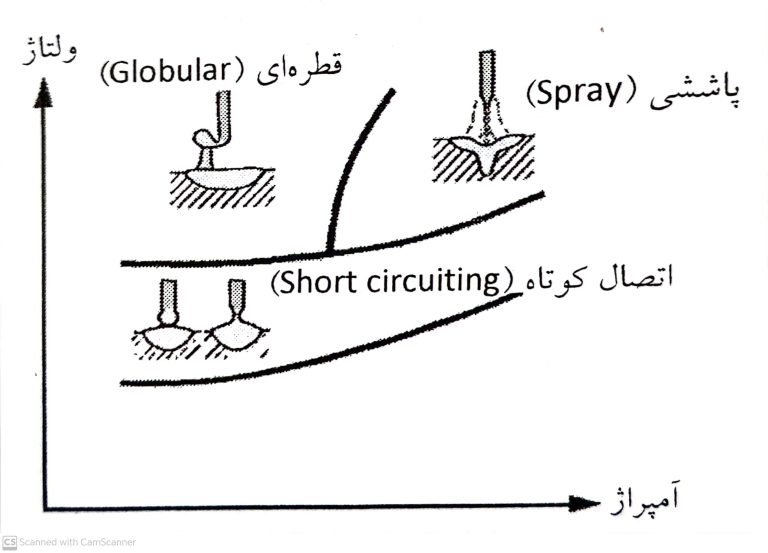
انواع انتقال مذاب در جوشکاری CO2
انتقال اتصال کوتاه قطرات در حداقل جریان الکتریکی لازم برای قطر مشخص سیم جوش صورت میگیرد. پس از تماس قطره ایجاد شده در نوک سیم جوش با سطح قطعه، اتصال کوتاه که با قطع شدن قوس الکتریکی همراه است، رخ میدهد و در این مرحله، قطره از سیم جوش به حوضچه جوش منتقل میشود. در واقع، در زمان برقراری قوس الکتریکی، هیچ انتقالی از فلز سیم جوش به قطعه کار انجام نمیگیرد. ایجاد یک حوضچه جوش کوچک که به سرعت منجمد میشود، از ویژگیهای این نوع انتقال است و این امر بهویژه برای جوشکاری قطعات نازک در وضعیتهای مختلف لبهسازی یا پلزنی و همچنین برای جوشکاری اتصالات با فاصله ریشه بزرگ بسیار مناسب میباشد. تماس سیم جوش با حالت اتصال کوتاه بین ۲۰ تا ۲۰۰ بار در هر ثانیه اتفاق میافتد.
ترکیب و نوع گاز محافظ تأثیر قابل توجهی بر اندازه قطرات تولید شده در نوک فرایند انتقال دارد. گاز دیاکسید کربن نسبت به گازهای خنثی، پاشش و جرقههای بیشتری ایجاد میکند، اما همچنین امکان نفوذ عمیقتری را نیز فراهم میآورد.
در این شیوه انتقال قطرات، به منظور تولید پاشش و نفوذ کافی در جوشکاری فولادها، پیشنهاد میشود که میزان نفوذ را هنگام جوشکاری فلزات غیرآهنی افزایش دهیم.
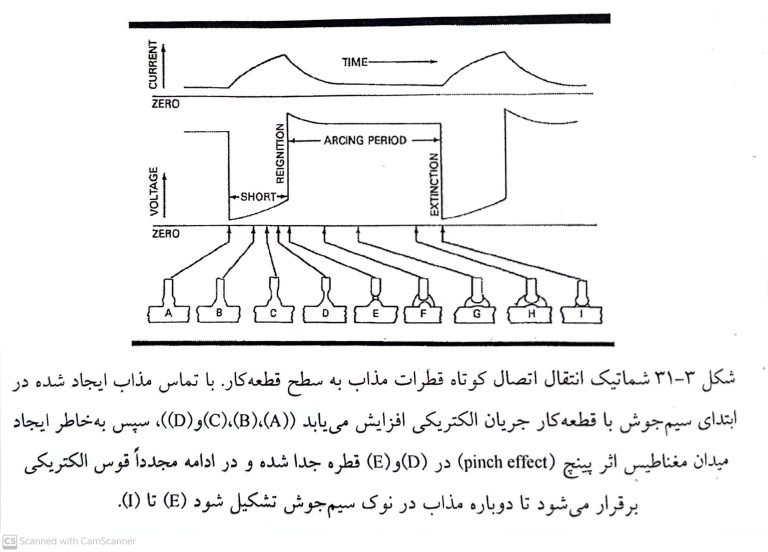
تصویر انتقال اتصال کوتاه قطرات مذاب به سطح کار
با اتکا به قطبیت DCEP که در الکترود به قطب مثبت منبع تغذیه متصل میشود، انتقال قطرات به شکل قطرهای در آمپراژهای نسبتاً پایین انجام میگیرد، بدون توجه به نوع گاز محافظ. در این شیوه انتقال مذاب، تأثیر گازهای محافظ به مراتب بیشتر است؛ به طوری که گازهای دیاکسید کربن و هلیوم میتوانند با اندکی افزایش در جریانهای الکتریکی، بیشتر از مقدار ضروری برای ایجاد اتصال کوتاه، موجب این نوع انتقال شوند.
حجم قطره مذاب در نوک سیم جوش افزایش مییابد و به اندازهای بزرگ میشود که از قطر سیم نیز فراتر میرود. این افزایش حجم به قطره کمک میکند تا به واسطه نیروی گرانش زمین، با سهولت بیشتری از سیم جدا شود. هرچند که بزرگتر شدن قطرات ممکن است به افزایش پاشش و جرقههای جوشکاری منجر گردد، اما این پدیده میتواند برای جوشکاری در سطوح صاف مناسب باشد. علاوه بر نیروی گرانشی، زمین به کمک نیروهای مغناطیسی نیز موجب جدایی مذاب از نوک سیم جوش میشود. این نیروها با حرکت دادن قطره مذاب فرآیند جدایی را تسهیل میکنند، اما در عین حال ممکن است باعث برخورد تصادفی قطره با سطح قطعه شوند که این مسأله میتواند به بروز عیوبی نظیر عدم ذوب یا نفوذ ناکافی منجر شود.
افزایش احتمال بروز عیوب ناشی از عدم ذوب کامل یا نفوذ ناکافی و همچنین حجم زیاد پاششها و جرقههای جوشکاری در این روش انتقال، آن را به گزینهای نامناسب برای جوشکاری تبدیل میکند. در تصویر زیر، این نوع انتقال قطرات مذاب به طور شماتیک نمایش داده شده است.
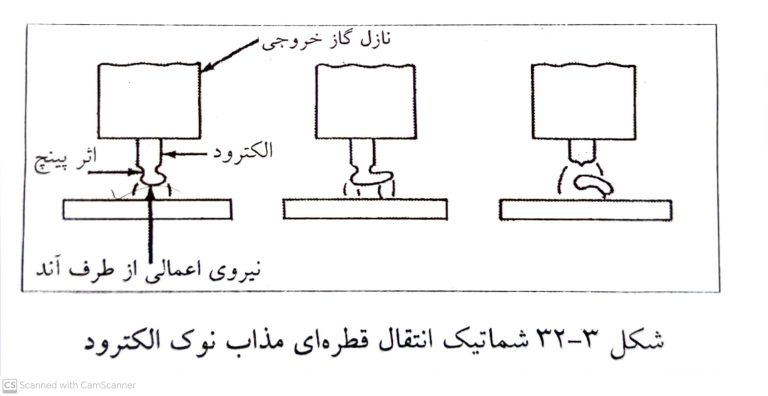
انتقال قطره ای مذاب نوک الکترود
استفاده از گاز محافظ آرگون خالص میتواند منجر به تولید نوع خاصی از انتقال قطرات شود که دارای پایداری و حداقل پاشش است. این نوع انتقال در جریانهای با قطبیت DCEP اتفاق میافتد و در هر ثانیه، حداقل یکصد قطره ریز از سیم جوش جدا شده و به طور منظم به حوضچه مذاب افزوده میشوند. حرارت بالایی که به قطعه کار منتقل میشود، باعث ایجاد حوضچه مذاب بزرگی میگردد که دارای سیالیت بالایی است و به سادگی قابلیت جریان دارد.
این روش جوشکاری به طور خاص برای موقعیتهای افقی و تخت کارایی دارد، اما در جوشکاریهای سقفی و عمودی عملکرد مناسبی ندارد. برای کسب اطلاعات بیشتر درباره انواع وضعیتهای جوشکاری، به فصل چهار مراجعه فرمایید. این نوع انتقال تنها در صورتی که از گاز خنثی آرگون استفاده شود، امکانپذیر است و میتوان از آن برای جوشکاری فلزات مختلف بهره گرفت. با این حال، به دلیل حرارت بالای ورودی در این روش، در صورت نازک بودن ورقها، ممکن است به جای جوشکاری، منجر به برش آنها گردد.
برای استفاده همزمان از مزایای انتقال اتصال کوتاه و اسپری که منجر به ایجاد قوسی پایدار و یکنواخت با حرارت ورودی کمتر به قطعه کار میشود، تکنیک جریانهای پالسی توسعه یافته و به کار گرفته شد. در فرآیندهای مبتنی بر این نوع جریان، همانطور که در تصویر زیر نشان داده شده، جریان زمینه اولیه باعث شکلگیری قوس الکتریکی و ذوب جزئی سیم جوش میگردد. سپس، با کاهش شدت پالس جریان، قطره بزرگتر میشود و در نهایت بدون ایجاد اتصال کوتاه، قطره جدا شده و به حوضچه جوش افزوده میشود. بعد از آن، جریان الکتریکی مجدداً افزایش مییابد تا با بالا رفتن انرژی قوس، قطرهای جدید در نوک سیم جوش تشکیل شود و این چرخه به طور مداوم ادامه پیدا میکند.
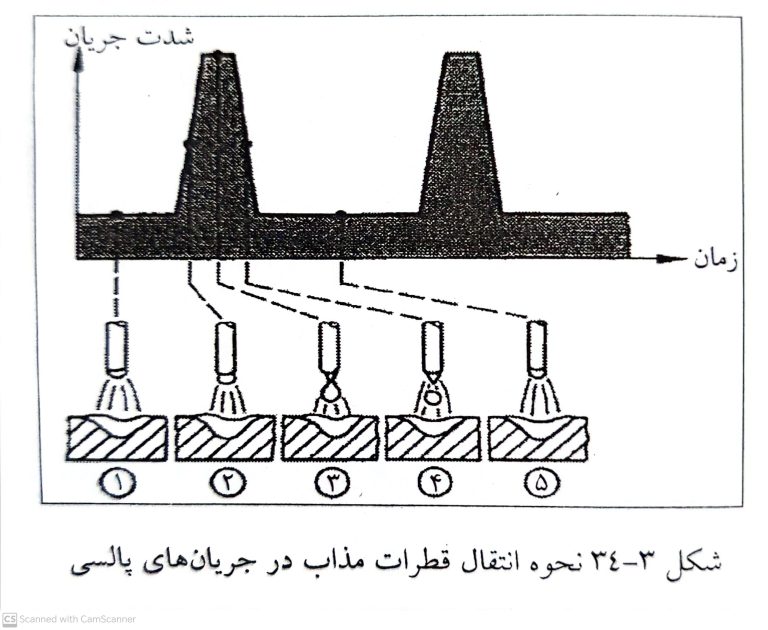
نحوه انتقال قطرات مذاب در جریان های پالسی
آشنایی با انواع سیم جوش های CO2
فلز پرکننده در فرآیند جوشکاری با قوس الکتریکی با گاز محافظ (GMAW) نه تنها به عنوان منبع فلز لازم برای ایجاد اتصال عمل میکند، بلکه باید الکترونها را نیز به نوک سیم جوش منتقل کند تا قوس الکتریکی شکل بگیرد. تنوع در ترکیب شیمیایی سیمهای جوش، نیاز به یک سیستم نامگذاری استاندارد را اجتنابناپذیر کرده است. سازمانها و انجمنهای مختلفی در این زمینه فعالیت کردهاند و از میان آنها میتوان به انجمن جوشکاری آمریکا (AWS) اشاره کرد. این انجمن در استانداردهای سری AS.XX، الکترودهای بیشتر فرآیندهای جوشکاری را مورد بررسی قرار داده است و فهرست استانداردهای مرتبط با این فرآیند در جدول ۲-۲ قابل مشاهده است. بر اساس این استاندارد، سیمهای جوشکاری فولادهای کربنی برای این روش طبق استاندارد 5.18 AWS به طور خاص دستهبندی شدهاند.
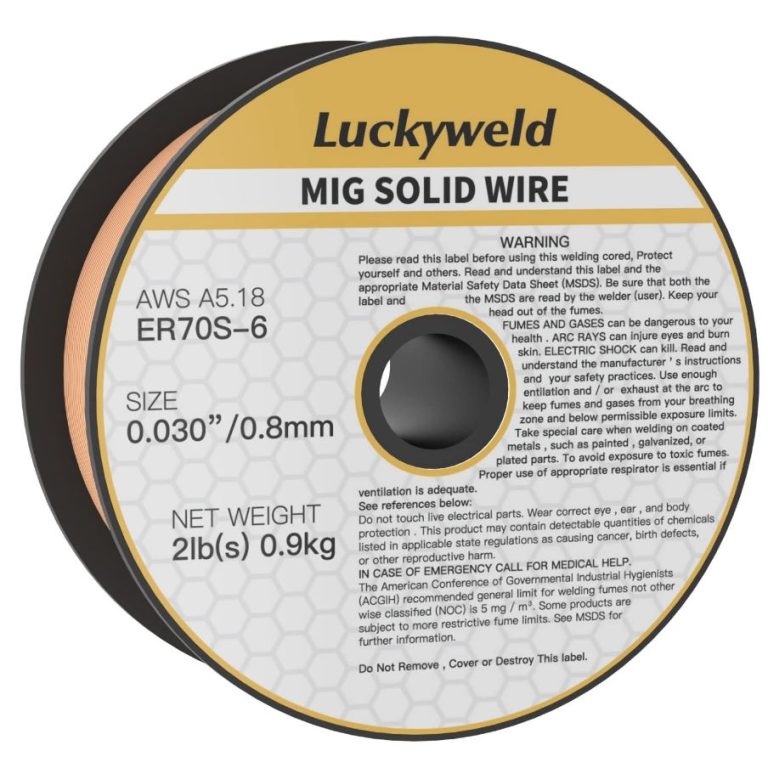
مشخصات روی سیم جوش CO2
مشخصات روی سیم جوش CO2
ER XX S-X N HZ
ER : مفتول سیم جوش
XX : حداقل استحكام كششی فلز جوش بر حسب Ksi
S :مفتول جامد فلزی
:X ترکیب شیمیایی فلز جوش یک عدد از ۲ تا ۷ و یا حرف G
N: مناسب برای جوشکاری تجهیزات هسته ای
:HZضریبی که مقدار هیدروژن را نشان میدهد .
شماره استاندارد یا مشخصه الکترودهای مورد استفاده در فرآیند جوشکاری CO2
شماره استاندارد یا مشخصه الکترودهای مورد استفاده در فرآیند جوشکاری CO2
در این فرآیند، معمولاً سیمهای جوش انتخابی با جنس فلزات پایه همخوانی دارند، اما برای ایجاد قوس پایدار و فراهم کردن شرایط مناسب برای زدودن اکسیژن از حوضچه مذاب، اندکی تغییر میکنند. در شرایط خاص، مانند جوشکاری فولادها و آلومینیومهای با استحکام بالا، ممکن است از سیمهای جوش متفاوتی که با جنس فلز پایه سازگار نیستند، استفاده شود. به عنوان مثال، در جوشکاری قوسی فلز گاز آلیاژ برنز منگنز، میتوان از سیمهای جوش آلیاژ مس روی، آلومینیوم برنز یا آلیاژ مس-نیکل-منگنز-آلومینیوم بهره برد.
قطر سیمهای جوشکاری در فرآیند GMAW نسبت به سایر روشها کوچکتر است. سایزهای معمولی این سیمها بین ۰٫۸ تا ۱٫۶ میلیمتر است، هرچند سیمهای با قطر ۰٫۵ میلیمتر و حتی تا ۳٫۲ میلیمتر نیز به کار میروند. به دلیل اندازه کوچک این سیمها و نیاز به جریانهای الکتریکی بالا، سرعت تغذیه آنها باید به میزان قابل توجهی بالا باشد. معمولاً سرعت تغذیه سیم جوش برای بیشتر فلزات بین ۴۰ تا ۳۴۰ میلیمتر در ثانیه متغیر است، اما فلز منیزیم به سرعتهای بیشتری، یعنی بالای ۵۹۰ میلیمتر در ثانیه نیاز دارد.
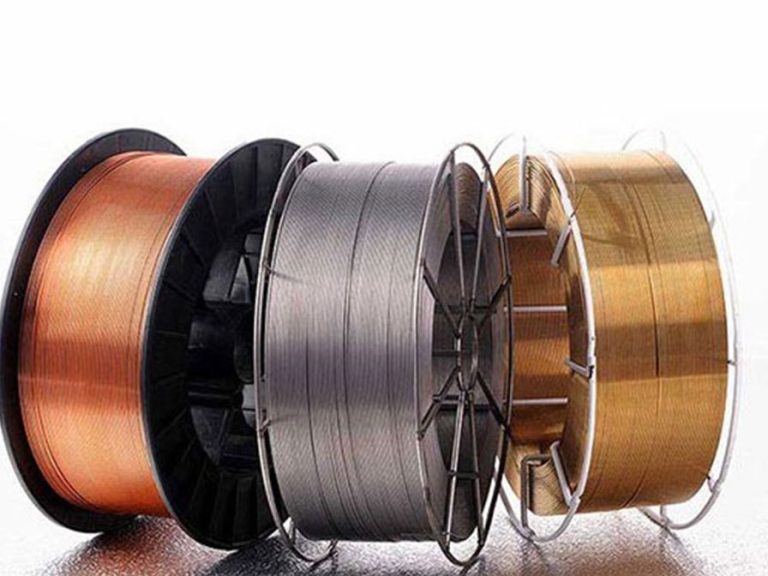
سیم جوشکاری CO2
سیم جوشکاری CO2
اگرچه نبود محدودیت در طول سیم جوش مصرفی، امکان جوشکاری فلزات مختلف در شرایط گوناگون بهصورت جوشهای پیوسته و بدون نقاط شروع و توقف مکرر را فراهم میآورد، که این امر به افزایش سرعت جوشکاری و رسوبدهی منجر میشود، اما این فرایند دارای مزایای دیگری نیز هست. از جمله این مزایا میتوان به حذف زمان لازم برای تعویض الکترود و سربارهزدایی و امکان استفاده از تجهیزاتی با نازلهای دو یا چند سیم جوشی اشاره کرد، که این موارد در مقایسه با جوشکاری قوسی با الکترود پوششدار، قابل توجه هستند. با این حال، محدودیتهایی مانند پیچیدگی بیشتر، هزینه بالاتر و قابلیت جابجایی کمتر تجهیزات، همچنین سریع سرد شدن فلز جوش به دلیل نبود لایه سرباره و حساسیت به وزش باد، که باعث میشود این روش در مکانهای غیرسقفدار چندان مورد استفاده قرار نگیرد، وجود دارد.
نتیجه گیری
این نوشته تنها یک مرور مختصر بر جوشکاری CO2 دارد و تلاش شده تا به جوانب کلیدی این روش پرکاربرد پرداخته شود. اگر علاقهمند به یادگیری این نوع جوشکاری هستید، میتوانید با مشاوران ما تماس بگیرید.
مطالب بیشتر :